Recently, Japan is striving to revive semiconductors by investing about 5 trillion won in its host plant in Japan to TSMC (the world’s best foundry company). Three countries, Intel in the U.S. and Samsung in Korea, are leading semiconductors, and Japan accounted for more than 50 percent of the world’s share in the 1980s. However, although Taiwan’s TSMC is the largest company in assembly production, it is still short of ultra-nano technology at a time when production and mass production of 3-nano 5-nano are set to take place. Samsung promotes the excellence of the ultra-nano process, Intel promotes ultra-nano mass production as the largest investment in the United States, and TSMC promotes maximum assembly production. However, I would like to talk about the current situation of the industry as a shortage of supplies after the current COVID-19 crisis.
As vehicle production, which had decreased significantly due to COVID-19 until the second quarter of 2020, has normalized since the second half of 2020, the supply of semiconductors for vehicles, which has soared suddenly, has not been able to keep up. As the global shortage of semiconductors for automobiles intensifies, the aftermath of the semiconductor shortage is spreading throughout the automobile industry, with major automakers cutting production. The semiconductor shortage faced by the auto industry at a time when it is about to recover from the damage caused by COVID-19 is expected to have a significant impact on the entire industry. We will learn about the current status and prospects of the shortage of semiconductors for vehicles that are hitting the automobile industry.Experts analyze that the current shortage of semiconductors for vehicles occurs for complex reasons. One of the main reasons is the rapid rise in demand for consumption home appliances, 5G mobile phones and communication networks, and games, IT platforms and devices in conjunction with COVID-19, increasing the demand for semiconductors essential for home appliances. On the other hand, the automobile industry struggled until the third quarter of 2020, due to the influence of COVID-19, so major semiconductor suppliers seem to have received orders for semiconductors for home appliances before semiconductors for vehicles and started production.
In a report published in February, IHS Markit, a global market research firm, also suggested an analysis that the current semiconductor shortage problem may have been predicted before 2020. The biggest reason is that the demand for microcontroller or microcontroller unit (MCU) chips in the automobile industry explodes, while few companies produce them. According to IHS Markit, the MCU is an average of 40 nanometers (40 nm) ultra-small chip, and the process of manufacturing this chip requires very high capital and technology. Therefore, there are limited factories that can supply MCU chips, and major semiconductor companies do not have their own factories but produce semiconductors through consignment production. Companies that develop semiconductor technology and design semiconductors without factories are called Fabless companies, and companies that manufacture semiconductors with factories are called Fab or Foundry. Currently, 70% of the world’s MCU share for automobiles is occupied by Taiwan Semiconductor Manufacturing Company (TSMC), a leading foundry (semiconductor consignment production), which is causing bottlenecks in supplying automobile MCUs as TSMC announces overall production restrictions in 2020.The MCU, which is made with minimal computer elements such as processors, memory, and input/output buses embedded in one integrated circuit, is an essential part for all electronic devices and has become an indispensable part for automobiles as automobiles have recently become electronic devices. Automobile MCUs are used in various parts of the vehicle, such as powertrain, chassis, electronic stability control device, body control module, and advanced driver support system (ADAS). Therefore, the shortage of semiconductors is expected to have a significant impact on primary suppliers that produce and deliver electronic control units (ECUs), which are mainly used in vehicles. Companies such as Bosch, Continental, and Denso, global primary automotive parts suppliers, make at least 30 different ECUs, and recently announced that there is a lack of supply of MCUs and analog direct circuits (ICs) purchased from outside.
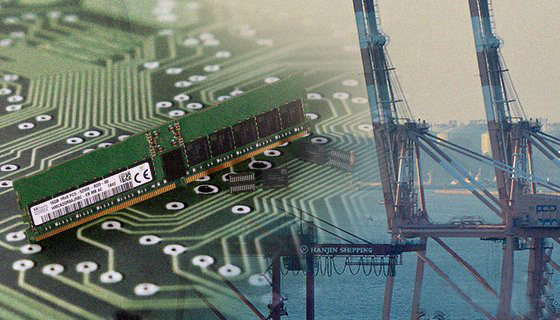
Considering the complex semiconductor manufacturing process, IHS Markit predicted that the current shortage of semiconductors for vehicles will not be resolved in a short period of time. Analysts say the semiconductor shortage will continue until the third quarter of 2021, and supply will be normalized only when semiconductor manufacturing plants rearrange their production capabilities and demand for consumer appliances subsides.The impact of the semiconductor shortage on the automobile industry began to become visible in earnest from the end of January. According to an analysis by IHS Markit as of January 29, the production of about 672,000 vehicles worldwide is expected to decrease in the first quarter of 2021 due to a disruption in semiconductor supply. In China alone, production of 250,000 vehicles is expected to be the most affected, and in North America, production of more than 100,000 vehicles is expected to be reduced.According to an analysis by AutoForcast Solution, an auto consulting firm, 85 auto factories worldwide suspended production for more than a day due to semiconductor supply until February 11, with 23 in North America, 26 in Europe and 36 in the Asia-Pacific region. In North America, carmakers such as Ford, Stellantis (FCA-PGA merger), Honda, and Toyota began to reduce production in January, and GM also decided to suspend three production plants in North America for a week in February.At a press briefing on Thursday, February 11, the White House promised to take “aggressive measures” to address the shortage of semiconductors for automakers in the U.S. White House spokesman Gen Psaki said the Biden administration is in talks with related companies and trading partners to identify bottlenecks in semiconductor supply and come up with immediate solutions, and plans to come up with comprehensive strategies to avoid supply bottlenecks that the semiconductor industry has faced for years in the long run. Also, according to Bloomberg News on February 18, Brian Deeds, the Biden administration’s top economic adviser, seems to be taking diplomatic measures to resolve the situation by sending a letter to Taiwan’s economy minister Wang Mei-hua on the semiconductor shortage issue. Bloomberg News predicted that President Biden would sign an executive order in the next few weeks to review the supply chain for major products at the pan-government level. The draft executive order reportedly includes a plan to review the supply chain of products such as semiconductor manufacturing and packaging, major minerals, medical supplies, and high-capacity electric vehicle batteries by the National Economic Council and the National Security Council.
Meanwhile, CEOs of 21 companies belonging to the Semiconductor Industry Association (SIA) sent a letter to President Biden on Thursday, February 11 urging the government to support companies that produce semiconductors domestically. The letter was co-signed by CEOs of major U.S. semiconductor companies such as Intel Corp., Qualcomm Inc., and Advanced Micro Devices Inc. The SIA stresses that U.S. companies’ global semiconductor share has fallen from 37% in 1990 to 12% now, calling for practical incentives for domestic semiconductor manufacturers to be included in Biden’s policy fund for “better reconstruction.” The United Auto Workers (UAW) also said in a statement this week that domestic production of important parts such as semiconductors needs to increase and urged the Biden administration to establish a trade policy that allows U.S. workers to produce high-tech products that rely on offshore procurement.In general, it takes 12 to 16 weeks to manufacture semiconductors, and in the case of MCUs, it takes 26 to 38 weeks of lead time. Currently, the lead time of almost all chips has been extended by one to two months due to a lack of supply, so experts predict that the shortage of semiconductors for automobiles will continue until the second quarter of 2021. Some analysts say that large foundry companies such as TSMC will not receive additional orders before the third quarter of 2021.
In an interview with the Detroit Trade Center, J Consultant at AutoForcast Solution said, “There seems to be no short-term solution to the current semiconductor shortage,” predicting that announcements will continue to suspend plant operations or reduce production over the next few weeks. It also diagnosed that the current situation has emerged as a structural problem caused by semiconductor companies using a “fab-light” strategy that gives more outsourcing to external foundry rather than expanding production lines and investing in equipment in the past.
Many automakers are expected to find alternative suppliers that can source semiconductors while adjusting production volume according to semiconductor supply for the time being. Therefore, it may be an opportunity for new companies to enter the market. In the era of self-driving cars, nearly 2,000 semiconductors are expected to be used in one vehicle, and the automotive semiconductor industry will play a key role not only in the current and long term of supply shortages. In Korea, many major conglomerates competing for the world’s No. 1 and No. 2 semiconductor technology are cooperating with mid-sized companies, and mid-sized companies are also throwing their hat into the semiconductor market for automobiles. Based on such solid technology, it is time for Korean auto parts makers to make efforts to find future food in the semiconductor market for automobiles.
Sam Kim
Asia Journal